ALL TYPES OF STANDARDS
There are various standards characterizing general necessities and test methods for various kinds of gloves. Here you will locate an overall perspective on every single current standard and classification.
CE CATEGORIES
Category 1
Gloves in this class are proposed to shield the user from nominal injuries that may happen during for instance washing, dishing yet additionally from hot items where temperatures are beneath +50C. Additionally appropriate for less gardening and other work where chance for lighter injuries.
Category 2
This category of gloves are expected to shield the user from injuries that are not categorized like negligible nor extremely high. The gloves must be marked with a pictogram indicating the gloves safety properties and are tried by the standard EN388, mechanical protection, at an authorized test organization. All classification 2 gloves are approved and type confirmed by a Notified Body to show the legitimacy of protection.
Category 3
Gloves in this group ensures protection against dangers that may cause intense outcomes, for example, death or permanent harm to health. The gloves must be marked with pictograms indicating the gloves safety properties and must be tried at an authorize test organization. They should likewise be approved and certified, for both kind and production control, by a Notified Body to show the legitimacy of protection. In Category 3, all chemical protection gloves are classified. In addition to it, heat protection can be arranged to this category.
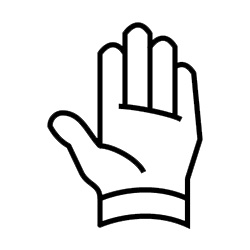
EN 420:2003 + A1:2009
SAFETY GLOVES – GENERAL REQUIREMENTS AND TRIAL METHODS
This standard characterizes the overall prerequisites legitimate for every single protective glove and sets requirements for glove marking.
The glove itself will not be a hazard to wear or cause harms to the worker.
The glove material will have a pH value somewhere in the range of 3,5 and 9,5.
The Chrome VI level in the glove leather must remain at 2,9 mg/kg or less.
On the off chance that the glove contains any substances known to cause allergic reactions, it will be expressed in the product information.
The glove sizes are uniform by minimum length.
EN 420:2003 + A1:2009 has no pictogram.
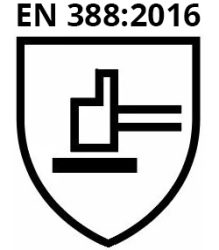
EN 388:2016
Protective gloves against mechanical dangers
As indicated by this regularity, attributes, for example, cut resistance, abrasion resistance, puncture resistance, tearing strength, and impact protection are tested. Four numbers and one, or two letters, will be shown related to the pictogram. These signs demonstrate the performance of the glove.
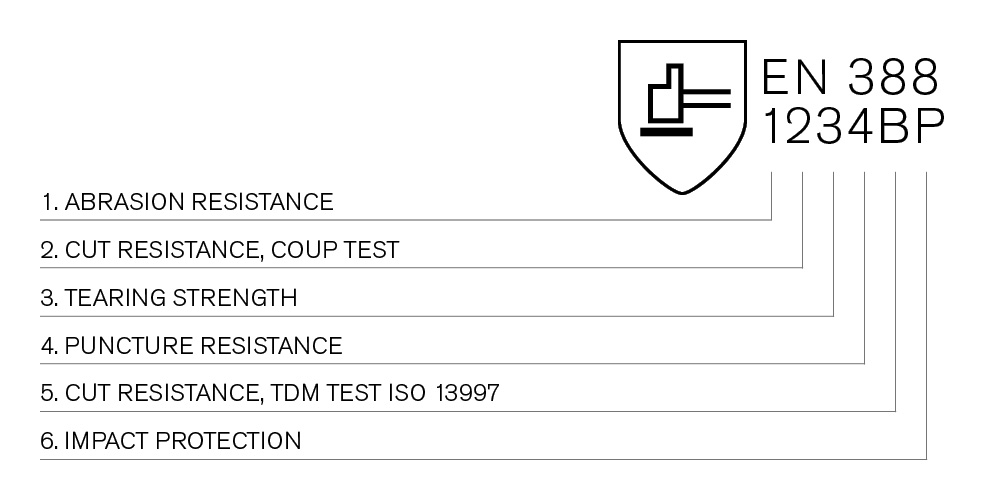
1. CUT RESISTANCE, COUP TEST
The cut security is tried. A blade is passed over the glove material until it slices through. The safety level is given by a number somewhere in the range of 1 and 5, where 5 demonstrates the highest cut protection. If that the material dulls the blade during this test, the cut test ISO 13997(TDM test) will be performed rather, see point 5.
2. ABRASION RESISTANCE
The material is subjected to abrasion by a sandpaper under a decided pressure. The protection level is shown on a size of 1 to 4 contingent upon the quantity of turns required until a gap shows up in the material. The higher the number is, the better the protection from abrasion.
3. PUNCTURE RESISTANCE
In light of the level of power required to puncture the material with a tip. The safety function is demonstrated by a number somewhere in the range of 1 and 4, where 4 shows the strongest material.
4. TEARING STRENGTH
The power required to tear the glove material is estimated. The protection level is demonstrated by a number somewhere in the range of 1 and 4, where 4 shows the solidest material.
5. CUT RESISTANCE, TDM TEST ISO 13997
If the blade gets dull during the coup test, see point 2, this test will be performed. The outcome is given by a letter, A to F, where F shows the most elevated level of protection. If any of these letters is given, this strategy decides the safety level rather than the coup test.
ISO 13997:1999 – Determination of resistance from cutting by sharp items.
An alternative cut test suggested for cut protection gloves. Will be utilized in EN388:2016 for cut protection gloves where the cut material dulls the cutting blade during testing. A blade cuts with steady speed however expanding power until breakthrough of the cut protection material. Level of safety is given in Newton, the power required for slice through at 20mm cut length.
6. IMPACT PROTECTION
If the glove has an impact protection, this data is given by the letter P as the 6th and last sign. In the event that no P sign, no impact protection is asserted.
EN 388:2003
This is the old version of the standard against mechanical dangers. The distinctions contrasted with the 2016 version are the paper grid in the abrasion test and how to perform testing of cut resistant fibers. Additionally, not applicable to test impact protection, there are as yet numerous protective gloves available named by the old version of this standard. These are as acceptable to use as the new marked gloves.
Imperative to comprehend is: it’s not the gloves performance that has changed. It is the method of testing the performance that has changed!

EN 511:2006
Protective gloves against cold
It is extra imperative to shield the hands from cold burns in cool situations. This standard measure how well the glove can withstand both convective cold and contact cold. Also, water penetration is tested after 30 minutes.
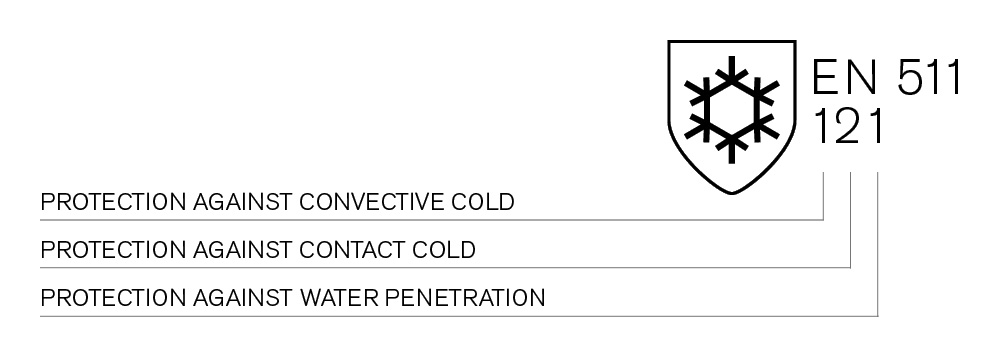
The first figure shows how well the glove protects against convective cold (performance level 0-4)
The second figure shows how well the glove protects against contact cold (performance level 0-4)
The third figure shows the glove protection against water penetration (performance 0 or 1 where 0 indicates “water penetration after 30 minutes” and 1 indicates “no water penetration after 30 minutes”)
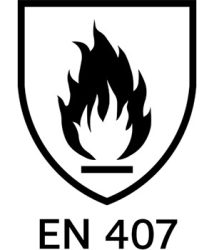
Protective gloves against thermal risks (Heat and/or fire)
This standard specifies demands and test methods for protective gloves that shall protect against heat and/or fire. The numbers given besides the pictogram indicates the gloves performance for each test in the standard. The higher number the better performance level.
This standard indicates demands and test techniques for safety gloves that will ensure protection against heat as well as fire. The numbers given with the pictogram shows the gloves performance for each test in the standard. The higher number the better its performance level.
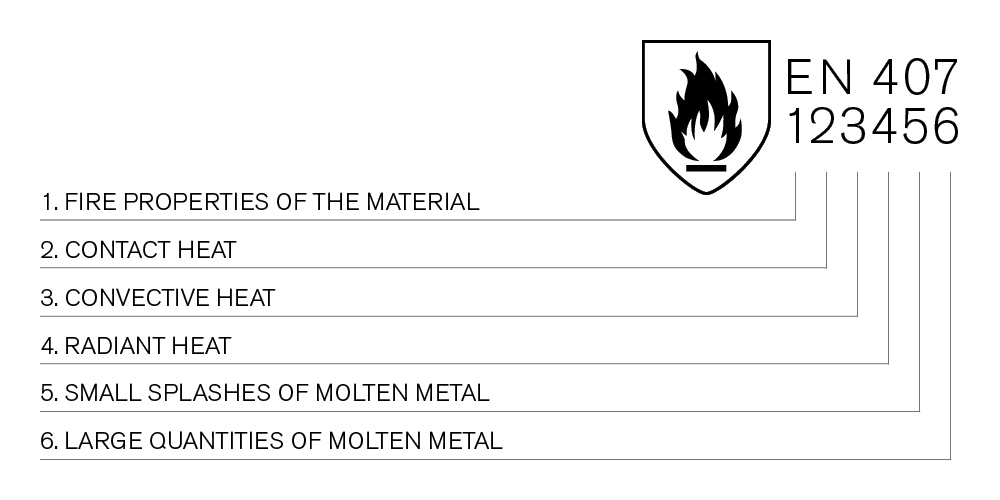
1. FIRE PROPERTIES OF THE MATERIAL
The start time and how long the material gleams or burns after start is estimated in this test. If the seam comes into pieces after a start season of 15 seconds, the glove has failed the test.
2. CONTACT HEAT
The glove is exposed to temperatures between + 100°C to + 500°C. Then it is measured how long it takes for the inner side of the glove to become 10°C warmer than it was from the start (about 25 ° C degrees). The glove must withstand the increasing temperature of maximum 10°C for at least 15 seconds for an approval.
3. CONVECTIVE HEAT
Here it is measured how long it takes to raise the inside temperature of the glove with 24°C, using a gas lubrication (80kW / m2).
4. RADIANT HEAT
The average time is measured for a heat permeation of 2.5kW / m2.
5. SMALL SPLASHES OF MOLTEN METAL
The test is based on the number of drops of molten metal that produces a temperature increase between the glove material and the skin with 40°C.
6. LARGE QUANTITIES OF MOLTEN METAL
A PVC film is attached to the back of the glove material. Molten iron is poured onto the material. The measurement consists of how many grams of molten iron required to damage the PVC film.
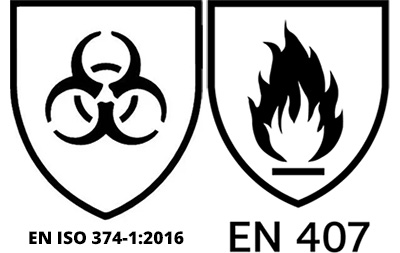
Protective gloves against dangerous chemicals and micro-organisms
Synthetic compounds can cause genuinely hurt for both the individual’ health and nature. Two Chemicals, each with known properties, can cause startling impacts when they are blended. This standard gives mandates of how to test degradation and permeation for 18 synthetic compounds however doesn’t reflect the genuine period of protection in the work environment and the difference between mixture and pure chemicals.
This standard determines the demands of the necessities for a glove to ensure protection against hazardous chemicals and micro-organisms.
The most limited suitable length that is fluid tight will compare to the base length of the gloves as determined in EN 420:2003 + A1:2009.
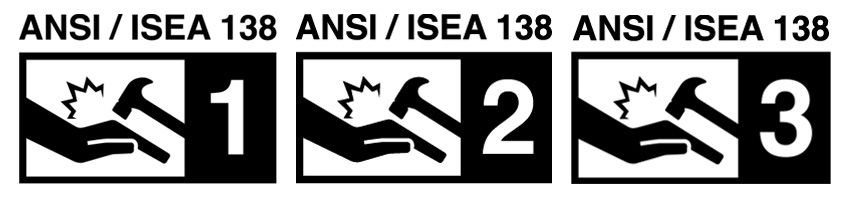
ANSI/ISEA 138-2019
Impact-resistant gloves
This American standard fixed requirements of gloves designed to protect the knuckles and fingers from impact forces.
The impact resistance is categorized in level 1, 2 and 3, where level 1 equals the lowest level of perforce and level 3 equals the highest level of performance. *tabell*
The test is performed by dropping a falling weight on the impact areas of the glove recording the force transferred in kilonewtons (kN). Areas tested are knuckles at back of hand, fingers and thumb.
*bild*
The weakest performance area describes the overall performance level of the glove and the protection level is given at the glove marking. *piktogram*